Packaging Quality Control
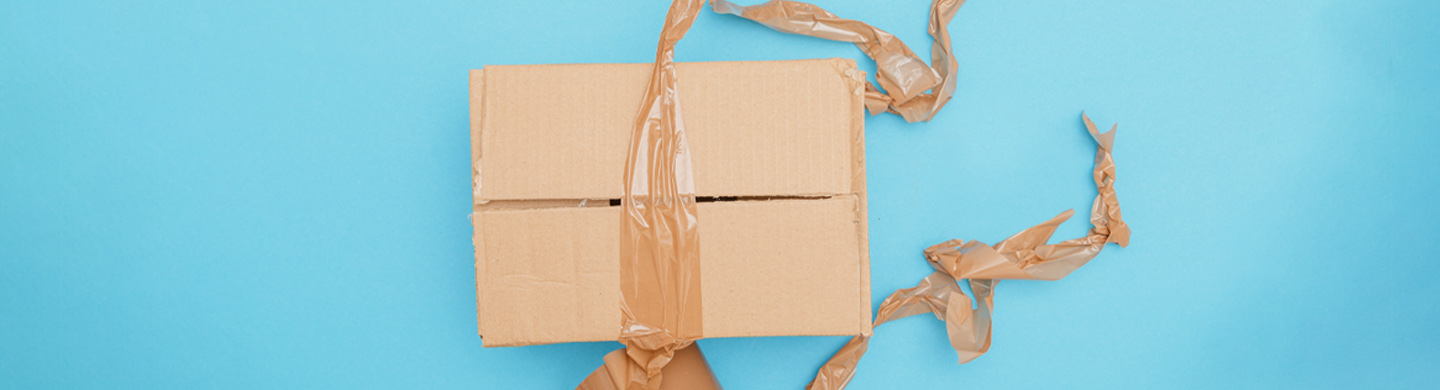
Minimize the negative impacts of packaging damage.
The most expensive and least sustainable package is one that fails to adequately protect the product as it moves through its distribution environment.
While repair, warranty and shipping costs may be the most obvious expenses caused by low quality packaging, packaging and products that take damage during shipping can harm a brand’s reputation with consumers and lead to hidden costs such as lost market share. Product and packaging waste from damaged goods, along with additional fuel consumption from reverse logistics, can have a significant impact on a company’s environmental footprint.
Thorough packaging quality control practices, paired with a quick and deeply analytical approach to identifying and remediating the sources of damage when it occurs, are the best ways to minimize the negative impacts of packaging damage.
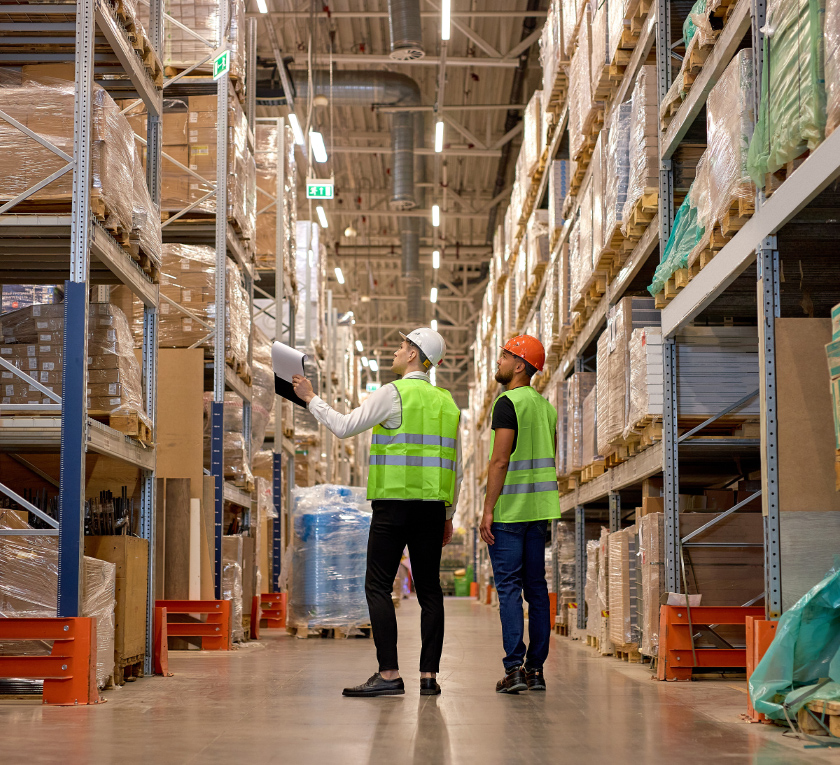
Thorough Threat Assessment
Good quality control starts with a thorough assessment of the threats to packaging integrity as the product moves from packaging line to the end user. A thorough risk assessment includes a review of all potential threats including regulatory challenges, selected materials, external hazards in the distribution environment, presence of hazardous materials in the product, product stability, ergonomics/user safety and sustainability impacts.
Packaging Testing Standards
With a thorough understanding of the potential risks to a product and its packaging, it becomes easier to identify the appropriate tests to validate packaging and ensure it protects the product against hazards it is likely to face during shipping. There is a wide variety of packaging testing standards to evaluate performance against different types of hazards it may face.
ASTM D4169 - Standard Practice for Performance Testing of Shipping Containers and Systems is a battery of ship testing methods with nearly 20 variations, allowing packaging teams to select the cycle that best matches the needs of their product and its distribution environment. These tests can evaluate many aspects of performance, including packaging fragility, ability to protect products against varying levels of vibration and many others.
ASTM issues many other testing standards, including ones that test performance at various altitudes, package leak testing, protection against temperature excursions, shelf-life studies and more.
The other major organization that issues testing standards is ISO, whose ISO 11607: Packaging for Terminally Sterilized Medical Devices standard provides important guidance for ensuring quality and packaging compliance with important regulations.
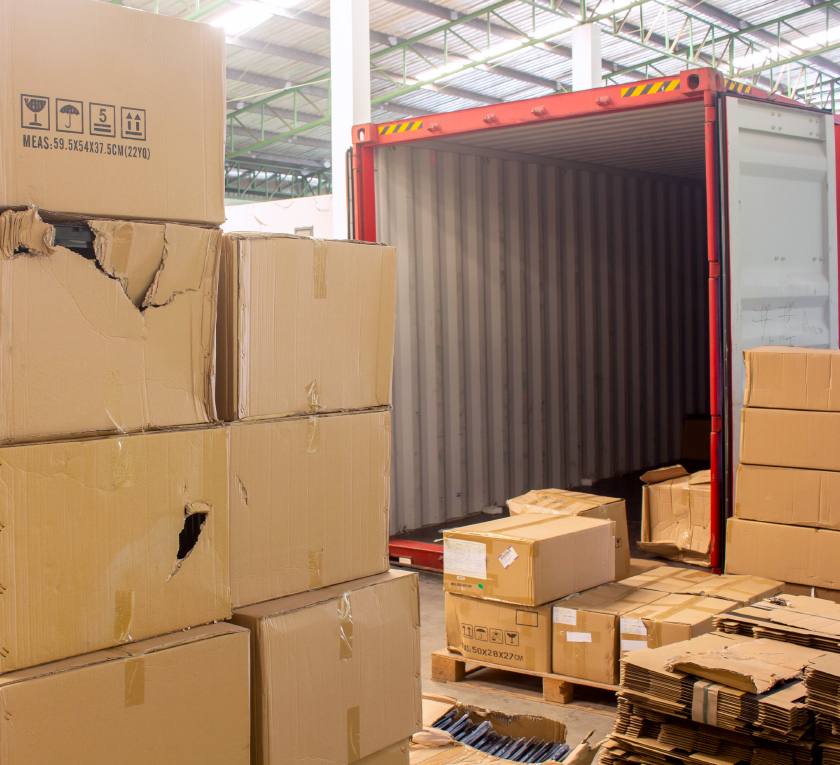
Remediate Packaging Issues
When quality issues arise, brands must act quickly to identify the root cause(s) of the problem and redesign packaging to better withstand them. Issues such as packaging transportation damage and sterile barrier systems failure call for immediate remediation. A thorough understanding of the source(s) of the issue and deep knowledge of packaging engineering principles enable rapid development of new packaging and inform which tests can be used to confirm the redesign addresses the weakness at the heart of the quality issue.
Hazards in the distribution environment aren’t the only source of quality issues in packaging. Sometimes issues may stem from an unforeseen change in the quality of materials from a supplier, a knowledge/training gap in new staff at a packaging facility or wear and tear that affects the performance of packaging equipment. These problems are often difficult to spot during routine operation of a packaging line, but they can be identified and avoided through regular packaging inspection, and the vigilance of leaders and staff on the packaging line.
Working closely with material suppliers to understand any changes in material properties in advance provides time for testing to ensure changes don’t impact performance. Input from equipment suppliers informs best practices for maintaining equipment to ensure it continues to work at a consistently high level. Thorough and well-maintained documentation of materials, packaging specifications and procedures can minimize the risk of problems due to knowledge gaps.
Contact Adept Group
Whether you need help evaluating risks in your supply chain, validating new packaging, remediating packaging quality issues or implementing ongoing quality control measures, the quality packaging specialists at Adept Group can help. Get in touch to learn more about how we can help ensure your packaging protects both your products and your brand’s reputation.